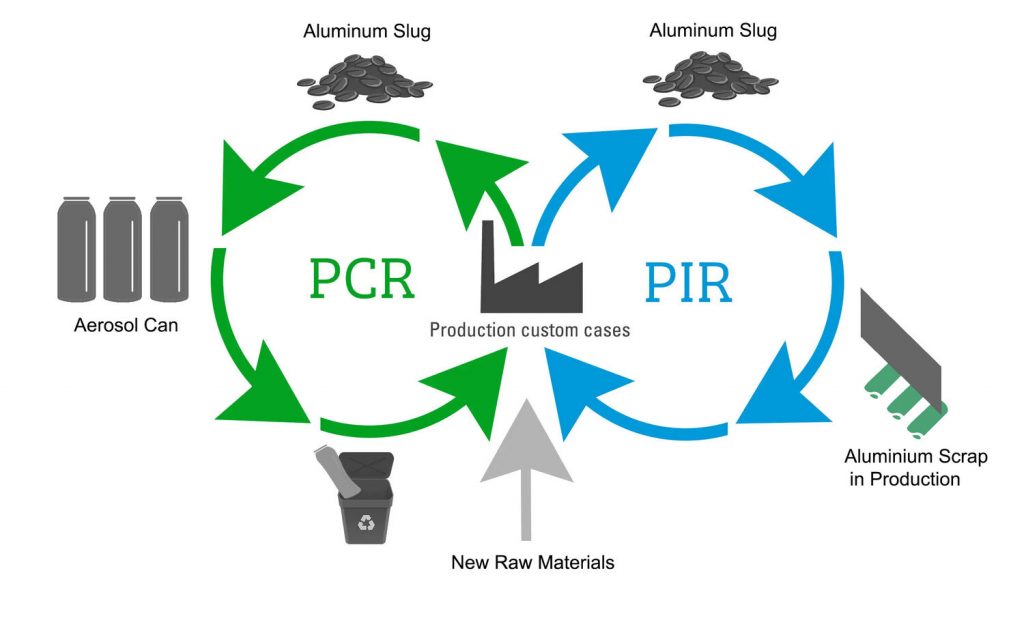
The global push for sustainable aluminum production has placed pir aluminum and pcr aluminum at the forefront of the packaging industry. These recycled materials are transforming the production of aluminum aerosol cans and aluminum bottles, offering a greener alternative to virgin aluminum. This article explores the intricate production process of PCR (Post-Consumer Recycled) and PIR (Post-Industrial Recycled) aluminum, detailing how raw materials are sourced, processed, and transformed into high-quality packaging solutions. By understanding these processes, stakeholders can better appreciate the role of green aluminum packaging in meeting environmental and market demands.
Sourcing Raw Materials for PCR and PIR Aluminum
The production of PCR and PIR aluminum begins with sourcing raw materials, a critical step in the aluminum recycling process. Each material has unique origins, which shape the complexity of their recycling:
Material | Source | Common Examples |
---|---|---|
PCR Aluminum | Consumer-discarded aluminum products | Beverage cans, aluminum foil, cables, lithographic plates |
PIR Aluminum | Industrial manufacturing waste | Cuttings, trimmings, defective aluminum slugs or sheets |
PCR aluminum is collected through municipal recycling programs or specialized facilities that sort aluminum from mixed consumer waste. This process requires robust infrastructure to ensure efficient collection and separation. PIR aluminum, by contrast, is gathered directly from manufacturing plants, where scraps like offcuts or rejected components are generated. Its controlled origin makes PIR aluminum less prone to contamination, simplifying the recycling process. Both materials are vital for producing eco-friendly aerosol cans and support aerosol can sustainability.
Step-by-Step Recycling Process
Transforming PCR and PIR aluminum into usable material for recycled aluminum manufacturing involves a series of carefully orchestrated steps. The process is designed to maximize efficiency while minimizing environmental impact:
- Collection and Sorting: PCR aluminum is sorted using technologies like eddy current separators, which isolate aluminum from plastics, glass, or other recyclables. PIR aluminum requires minimal sorting, as it is collected directly from production lines.
- Cleaning and Pre-Treatment: Both materials are cleaned to remove contaminants such as paints, coatings, or organic residues. PCR aluminum often demands more intensive cleaning due to its exposure to consumer environments, while PIR aluminum benefits from its cleaner industrial origin.
- Melting and Purification: The cleaned aluminum is melted in high-efficiency furnaces. PCR aluminum is typically processed in double-chamber furnaces equipped with smoke filtration systems to handle impurities and reduce emissions. PIR aluminum, with fewer contaminants, may use single-chamber furnaces for faster processing.
- Alloying and Casting: The molten aluminum is alloyed with elements like magnesium or silicon to enhance strength and durability, then cast into ingots or slugs. These are tailored for applications like aluminum aerosol cans or aluminum bottles, with a minimum purity of 99.5% to meet industry standards.
- Rolling and Forming: The ingots are rolled into thin sheets or extruded into slugs, which are then shaped into aerosol cans or bottles using precision manufacturing techniques.
This streamlined process ensures that recycled aluminum retains the quality needed for high-performance packaging while supporting green aluminum packaging goals.
Technological Advancements in Aluminum Recycling
Innovations in recycling technology have significantly improved the efficiency and sustainability of PCR and PIR aluminum production. Key advancements include:
- Advanced Sorting Systems: Technologies like laser-induced breakdown spectroscopy (LIBS) enhance the accuracy of aluminum sorting, reducing contamination in PCR aluminum streams.
- Energy-Efficient Furnaces: Modern furnaces use regenerative burners and advanced filtration to cut energy consumption and emissions by up to 30% compared to traditional models.
- Inline Quality Control: Real-time spectrographic analysis ensures that the aluminum meets stringent purity and composition standards, critical for food-grade eco-friendly aerosol cans.
These technologies enable the industry to produce high-quality recycled aluminum with minimal environmental impact, aligning with global sustainability trends.
Challenges in Producing PCR and PIR Aluminum
While PCR and PIR aluminum are game-changers for sustainable aluminum production, their production faces several hurdles:
Supply Chain Complexities
PCR aluminum production relies on complex supply chains involving waste collection, sorting, and transportation. Variations in recycling infrastructure across regions can lead to inconsistent supply or quality. Industry associations like the International Aluminium Institute advocate for standardized collection systems to address these challenges.
Contamination Management
PCR aluminum is susceptible to contamination from non-aluminum materials or chemical residues, requiring rigorous cleaning and testing. Advanced pre-treatment processes, such as de-coating systems, are employed to ensure the material meets the purity standards for recycled aluminum manufacturing.
Cost and Efficiency Trade-Offs
Processing PCR and PIR aluminum can be costlier than using virgin aluminum due to the energy and labor involved in sorting and cleaning. Additionally, PIR aluminum may need to be blended with virgin aluminum to achieve specific mechanical properties, which can complicate cost structures. However, the long-term savings from reduced raw material dependency and regulatory compliance offset these costs.
Benefits of PCR and PIR Aluminum Production
The production of PCR and PIR aluminum offers compelling advantages for the packaging industry:
Benefit | Impact |
---|---|
Energy Efficiency | Recycling aluminum uses 95% less energy than virgin aluminum production, lowering operational costs. |
Reduced Emissions | PCR aluminum generates 0.8 kg CO2e/kg, compared to 9.1 kg CO2e/kg for virgin aluminum, enhancing aerosol can sustainability. |
Consumer Appeal | Products made with pir aluminum and pcr aluminum resonate with eco-conscious consumers, driving demand for green aluminum packaging. |
Resource Conservation | Recycling reduces the need for bauxite mining, preserving natural ecosystems. |
These benefits make PCR and PIR aluminum ideal for producing packaging solutions like aluminum bottles used in cosmetics, pharmaceuticals, and personal care products.
Conclusion
The production of PCR and PIR aluminum is a cornerstone of sustainable aluminum production, enabling the creation of eco-friendly aluminum aerosol cans and aluminum bottles. From sourcing raw materials to leveraging cutting-edge recycling technologies, the process balances efficiency, quality, and environmental responsibility. Despite challenges like supply chain complexities and contamination, the benefits of reduced emissions, energy savings, and consumer appeal make recycled aluminum a vital component of modern packaging. In the next article, we’ll explore how PCR and PIR aluminum are applied in aerosol can manufacturing, highlighting their practical advantages in real-world scenarios.